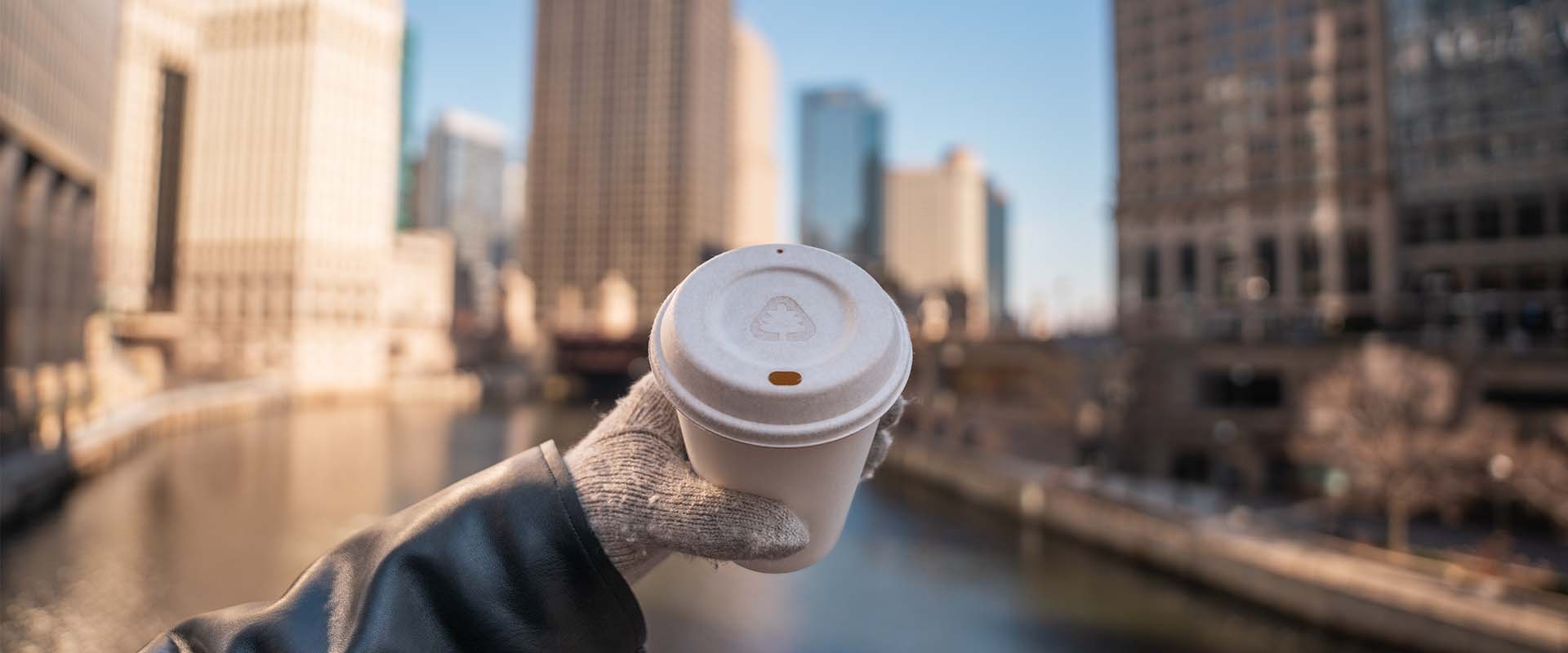
what is the right fit
For your packaging needs?
Dry Molded Fiber may not be the answer to every packaging challenge, but where it fits, it delivers exceptional value.
What is the right fit for your packaging needs?
Dry Molded Fiber may not be the answer to every packaging challenge, but where it fits, it delivers exceptional value.
Resource efficiency and freedom to design
We work with various industries, and we’re not here to wage war against other technologies, It’s about choosing the right solution for the right product. Dry Molded Fiber can complement your existing packaging production — whether it’s plastic, traditional fiber-forming, or other methods. Many of our customers successfully integrate it to expand their product range and capabilities.
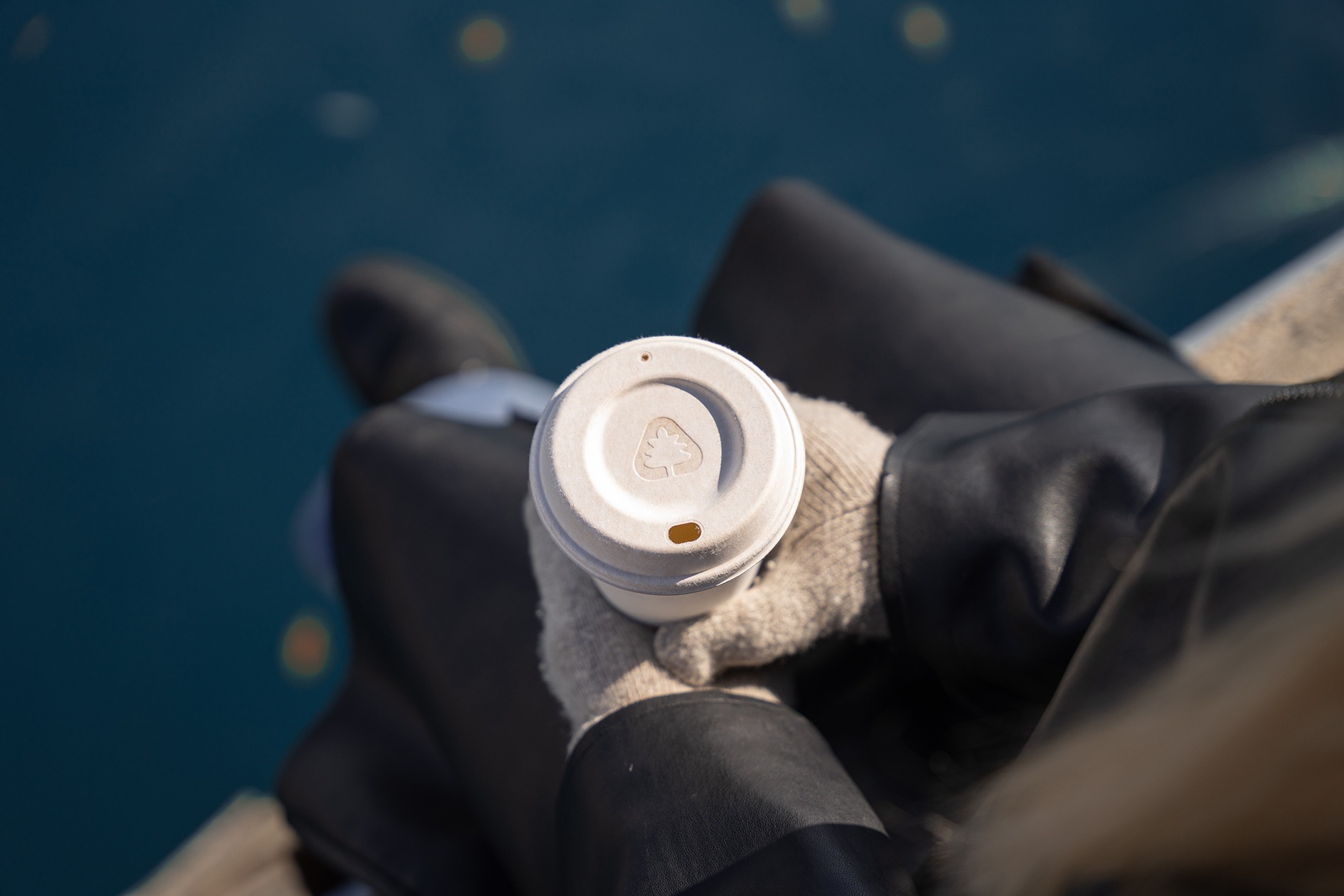
Dry Molded Fiber uses minimal water and energy, while maximizing raw material efficiency, making it a responsible choice for companies aiming to reduce their environmental impact. It enables the production of renewable, recyclable, compostable, and biodegradable items — ensuring that sustainability goals are met without compromising performance.
Our technology enables seamless integration of advanced design features — color, labels, patterns, whole punching, stacking, de-nesting, and hinges all in one in-line stroke, with no extra production steps. This opens new possibilities for fiber-based products and creative possibilities for brands.
Speed and high conversion in minimal floorspace
In terms of cycle time, we’re down to 3.5 seconds in the PulPac Modula, and 3.8 seconds in the PulPac Scala. The Modula converts 2.6 metric tons/24 hours for coffee lids, while the Scala, despite its compact size, handles just under 1 ton/24 hours. The beauty of our machine platforms is that it’s the press size that limits conversion rates, meaning a larger press can increase output.
Factory space is a significant cost driver in production, and when paired with conversion rate, it becomes a critical success factor. Our machine platforms are effective in both areas as there’s no need for additional material preparation before converting. It’s a streamlined process—raw material to finished product in a single machine.
In the end, Dry Molded Fiber offers a unique combination of advantages — whether for high-volume production, unique customer orders, specific design needs, or optimizing factory footprints. You can start at your own pace, whether by evaluating the technology, complementing your existing production, or scaling it up to full capacity.
“My team and I will guide you through every step – from validating if Dry Molded Fiber is the right fit, to helping you select the best machinery, whether it’s the high-output PulPac Modula or the compact PulPac Scala. Our approach is simple: we provide the insights you need to make the right decision, and if our technology isn’t the best solution, we’ll let you know. We’re committed to helping you get the best results.” – Sanna Fager, Chief Commercial Officer at PulPac
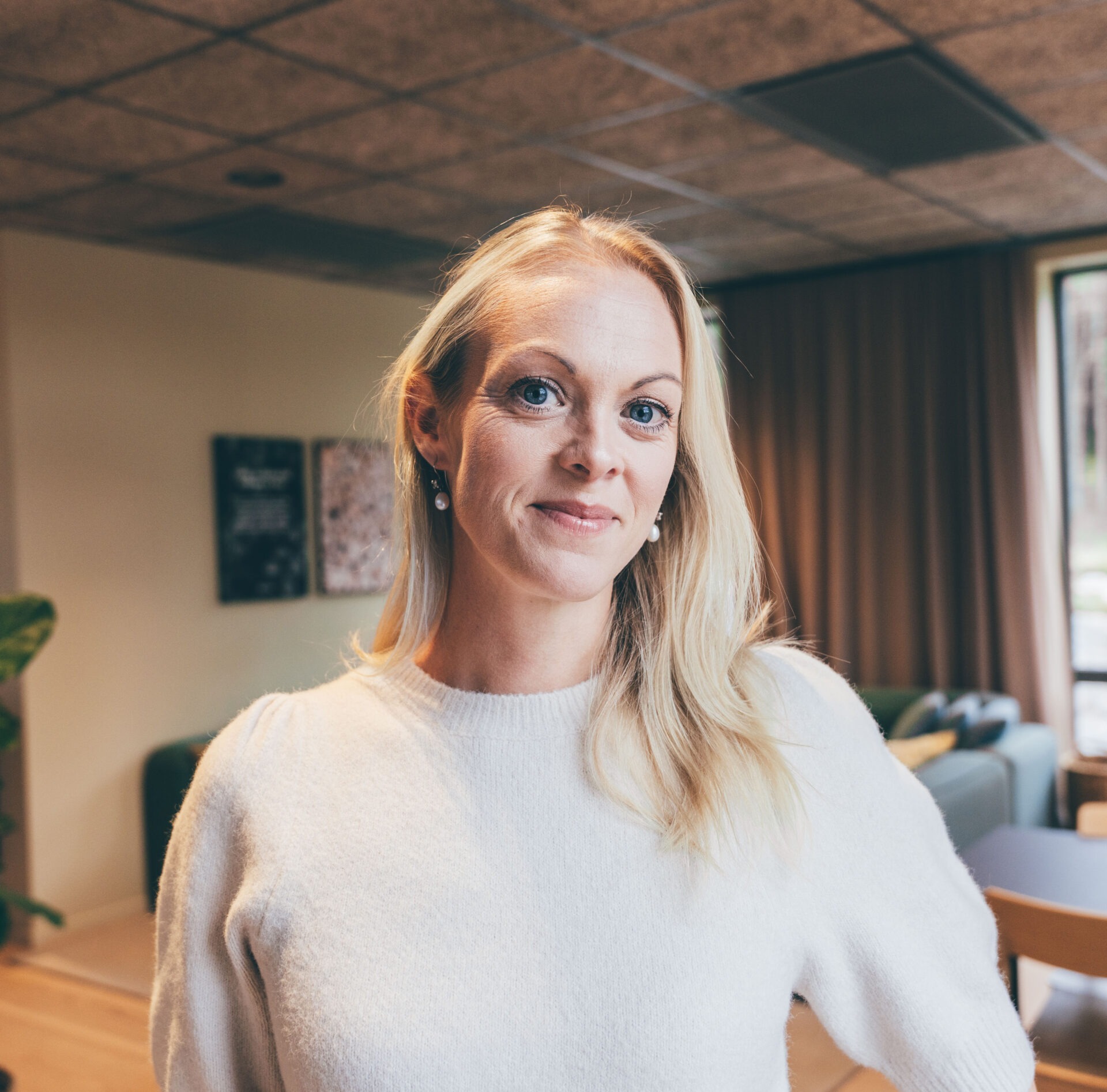
“with our licensing model, your success is our success – we only win when you win.”
– Sanna Fager, Chief Commercial Officer