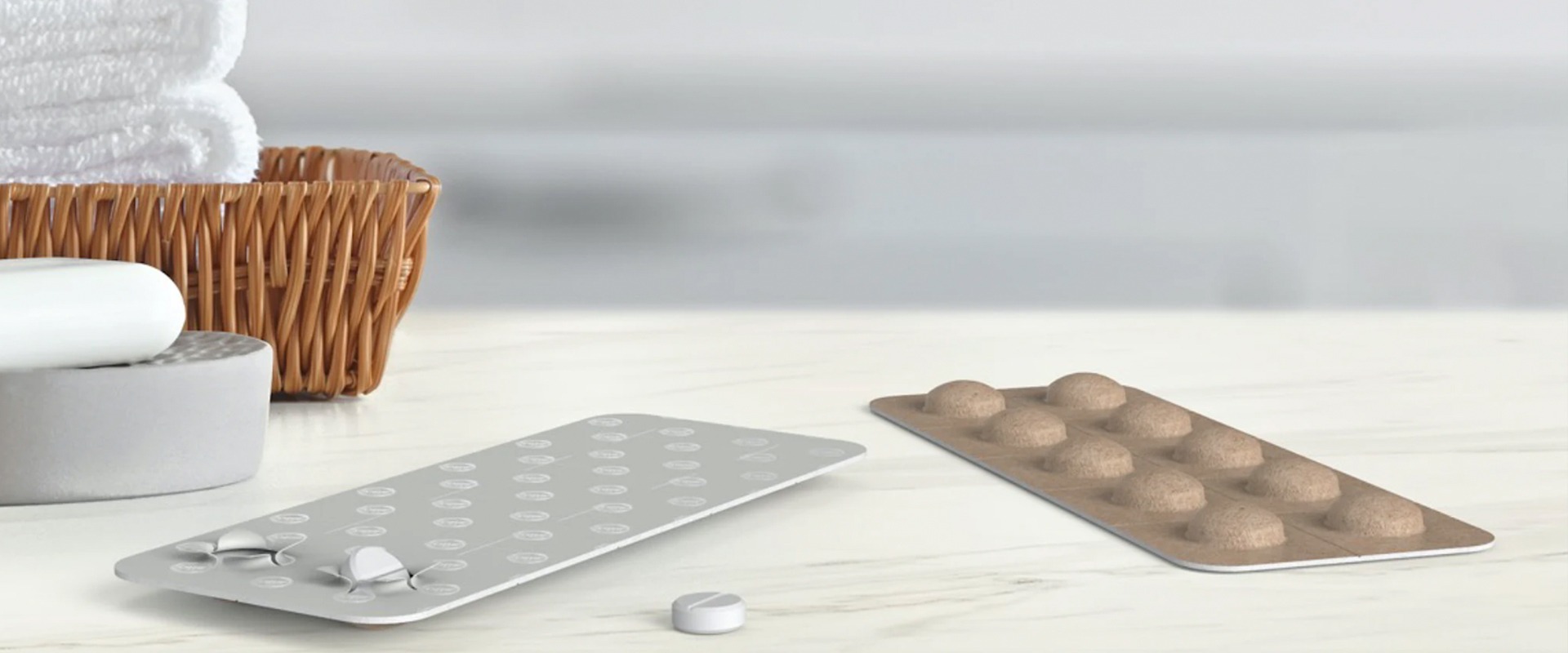
The Blister Pack Collective
Eliminating PVC and other plastics in tablet packs
PA Consulting and PulPac have seeded the collective and developed the underlying technology needed to bring a functioning Dry Molded Fiber tablet blister pack to life.
Join the Blister Pack Collective
Calling all pharma, consumer health, and FMCG businesses — join the Blister Pack Collective from PA and PulPac to create the world’s first planet-friendly, Dry Molded Fiber tablet blister pack.
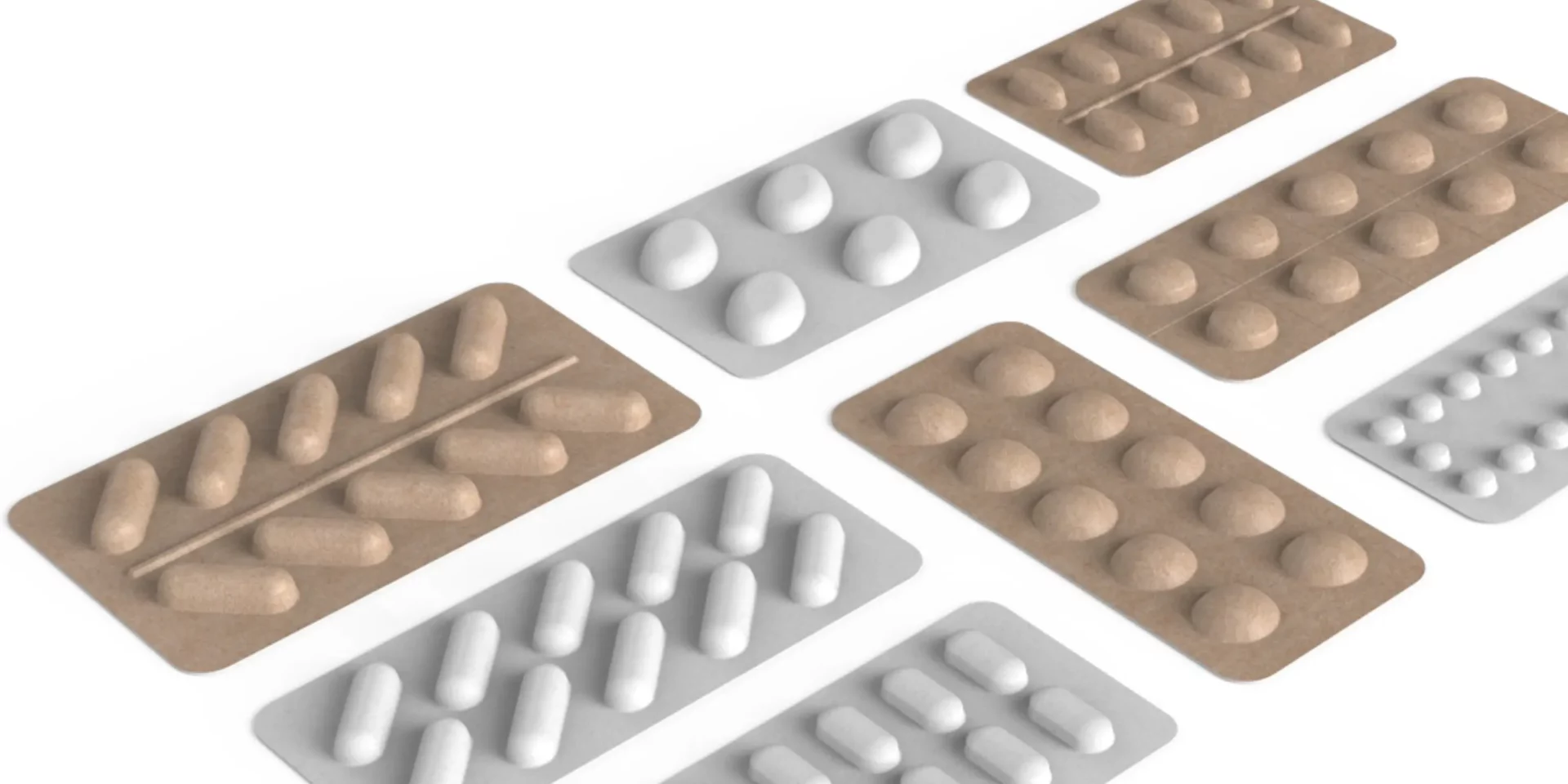
Brands that joined
The Blister Pack Collective
Haleon, Sanofi, and Bayer have all joined the Blister Pack collective. They are now utilising the Dry Molded Fiber technology to develop blister packs that eliminate or minimise the use of plastics in over-the-counter prescription drugs and nutraceuticals.