
The genesis of PulPac
Where it started and how it's going
The genesis of PulPac
Let’s start by getting the elephant out of the room: PulPac does not have a beef with plastic. In many ways, plastic is a fantastic invention: a persistent material capable of lasting several lifetimes. But why use it for products only meant to last a few minutes, hours, or weeks? We see how plastic affects the environment when it ends up where it shouldn’t. And we came up with an innovation to solve, or at least slow down, the negative climate impact of packaging.
Where it started and how it’s going
During the 1950s, plastic became “the material” for the future. It offered never-before-seen possibilities applicable to almost any use area. But more importantly, it provided speed, high output, and cost-efficiency. And that’s how it became the preferred manufacturing method. Today we know of its effects. Still, global consumption and plastic production are increasing. And unfortunately, estimates show no signs of it slowing down, making plastic pollution one of the toughest challenges today.
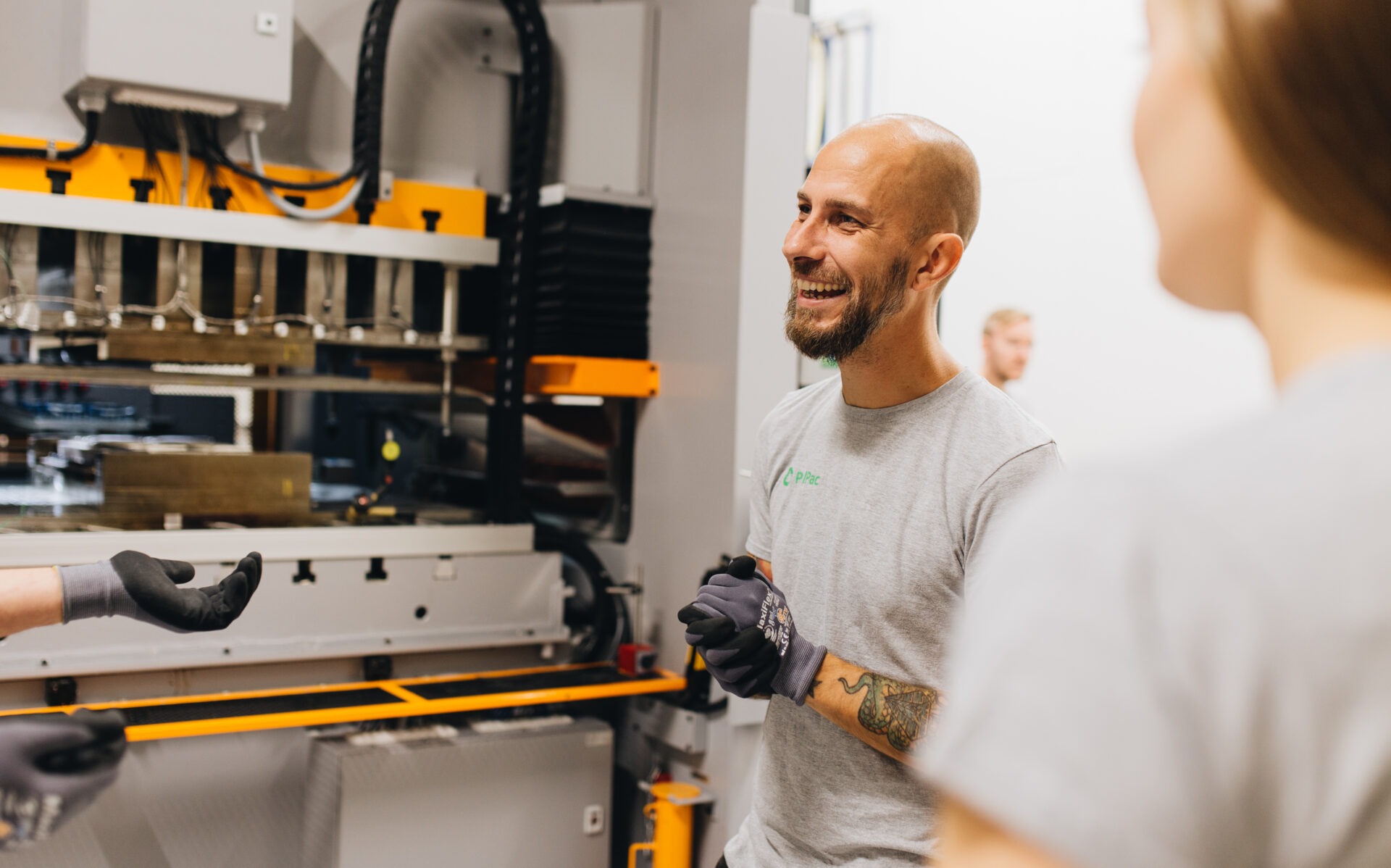
While we are pretty good at handling plastic waste in some parts of the world, a lot of plastic ends up in the garbage bin and, subsequently, in landfills. It’s no wonder why recycling still struggles to keep up with what we produce. In Europe, only 30% of the yearly production gets collected or recycled. The remaining 70% ends up having a severe impact on ecosystems and biodiversity in our environment and our oceans. An EU Commissions study from 2018 shows that plastics alone, especially from single-use products, account for a mind-blowing 85% of the world’s marine litter*.
Because second to none still doesn’t cut it
Tried, true, trustworthy, and often regarded as “sustainable.” For over a century, wet molding has been the go-to method for turning cellulosic fiber into packaging. However, a slow manufacturing process and hefty water use make wet molding inefficient and expensive, adding to social and environmental impact. Plus, wet molding requires heat, which requires electricity to dry the products. So, the better alternative still isn’t good enough. However, paper products have a high recycling rate. But since it’s biodegradable, it has a lower environmental impact.
Dry Molded Fiber is an ingenious and simple solution to an unnecessary problem
The climate threat is real, and unfortunately, we have to give it some credit for inspiring the development of Dry Molded Fiber. The impact of single-use packaging items is one of today’s more significant challenges. And there is, unfortunately, no evidence of it slowing down.
So, we developed a technology based on fiber-forming principles — like wet-forming. But we figured out how to take almost all the water from the equation. With Dry Molded Fiber, we provide plastic converters and the packaging industry with a solution for sustainable, responsibly produced packaging with lower climate impact and high recyclability.
*European Commission, 2018b: https://ec.europa.eu/environment/circular-economy/pdf/plastics-strategy.pdf

“We developed a technology based on fiber-forming principles — like wet-forming. But we figured out how to take almost all the water from the equation.”