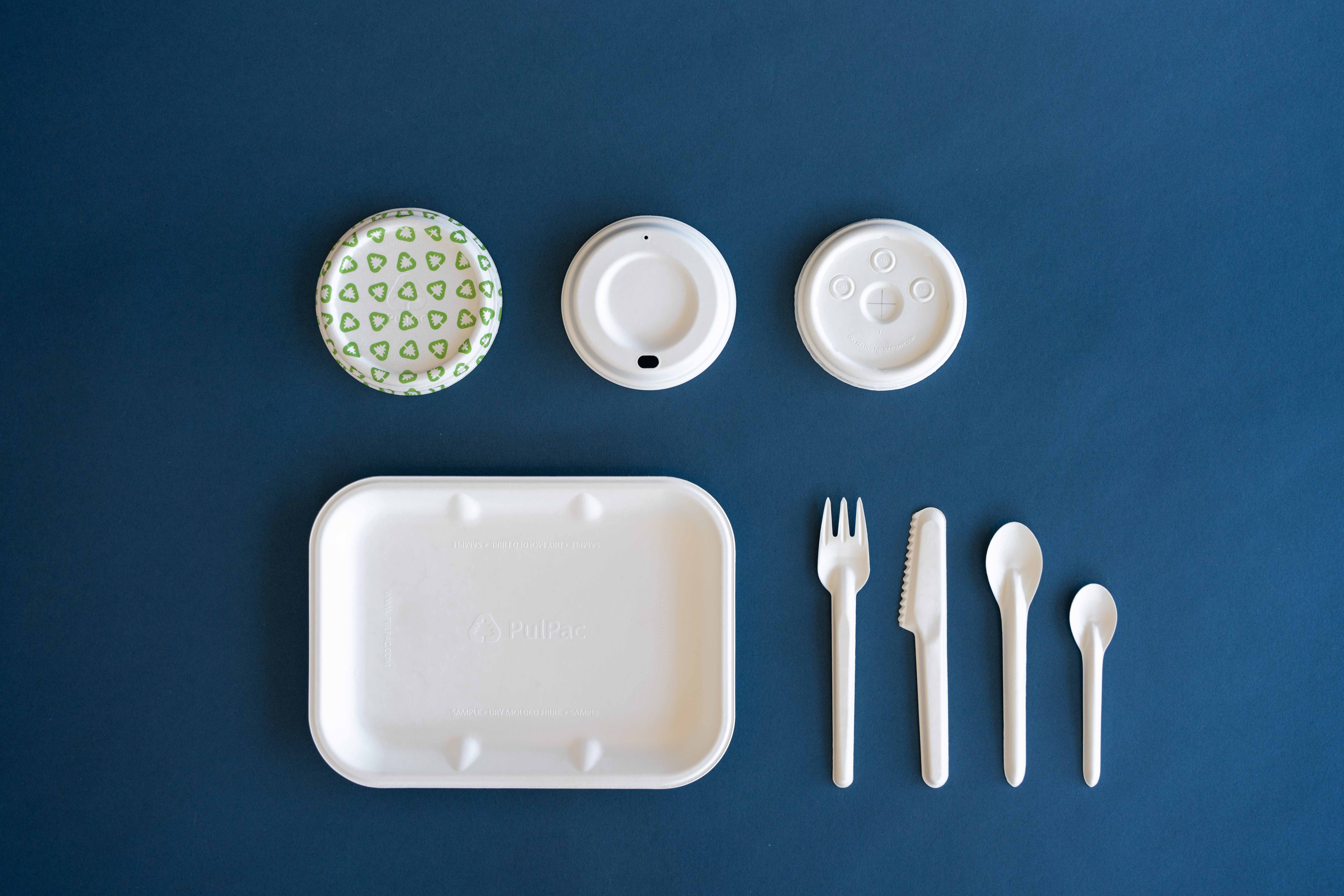
Dry Molded Fiber products ready for production
The PulPac Highway Application Program is a range of standardized and commercially validated applications ready for production by PulPac’s licensees.
Standardized and commercially validated Dry Molded Fiber products ready for production
The PulPac Highway Application Program is a range of standardized and commercially validated applications ready for production by PulPac’s licensees. First validations confirm that Dry Molded Fiber cutlery is circular into existing paper-recycling streams, that they biodegrade if misplaced, and have a climate impact that is only a small fraction compared to single-use plastic cutlery (~15%). Cutlery, trays, and lids are first out, but additional Highway Applications will follow.
Compared to other fiber forming methods, PulPac’s Dry Molded Fiber technology uses almost no water, significantly less energy and is up to 10 times faster – offering unit economics that can compete with plastics.
“The planet needs fewer excuses and more action.”
— Sanna Fager, Chief Commercial Officer PulPac
The PulPac Highway Application Program is spearheaded via an R&D consortium and co-financed by Vinnova’s ‘Scale-up of Sustainable Industry’ initiative. To date, the Highway Application Program has designs ready for protective lids, coffee cup lids, cold drink lids, cutlery, and trays. Additional products with a set design, tooling, material and barrier solution are in development.
“Time is increasingly becoming the most important factor in dealing with environmental challenges. Leading FMCG brands must move from pledges and promises to action – and the packaging industry need to make real-world progress. By creating a range of standardized highly demanded products, that are commercially and environmentally validated, we can help our customers speed up the transition towards sustainable fiber-based packaging and a greener, cleaner world,” says Sanna Fager, Chief Commercial Officer PulPac.
As part of the program, RISE recently presented a recyclability report and climate impact study for Dry Molded Fiber spoons. Results confirm that the spoons are biodegradable, have excellent recyclability and that climate impact is 2.5 g CO2eq per spoon (3.8g each) or about 0.66 kg CO2eq per 1 kg product. As a comparison, in an LCA by Takou et al. (2019), with focus on single use plastic products in Denmark, the climate impact of an average polypropylene (PP) cutlery with similar weight was about 15 g CO2eq per piece or about 4.2 kg CO2eq per 1 kg product. The main climate impact in Dry Molded Fiber cutlery comes from the production of input materials fluff pulp and tissue. The actual Dry Molded Fiber production process stands for a mere 7% of the climate impact.
“As our customers work to balance environmental concerns with business performance, sustainability is top of mind – but it’s time to speed up efforts. The planet needs fewer excuses, and more action. Together with partners, we can present a turn-key production platform, and a range of highly demanded, ready to produce applications with very competitive unit economics and unmatched sustainability features. Next generations deserve new generations of packaging – where sustainability is just a given” Sanna Fager concludes.
Media Contacts
About PulPac
We are the inventors of Dry Molded Fiber Our groundbreaking technology helps producers within the packaging industry to swiftly transition toward circularity. With our cost-competitive, fiber-based alternative, they meet the market and planet’s needs for responsibly produced packaging but also gain leverage from spearheading the industry. We build a community with our global partner network to ensure we reach our goals.
About Dry Molded Fiber
A brilliantly simple solution for packaging producers to meet the market’s and planet’s needs for responsibly produced packaging. Dry Molded Fiber enables a swift transition towards circularity, with a cost-competitive, fiber-based alternative. Turns ordinary pulp into any rigid, three dimensional product, using almost no water. And it’s fast!