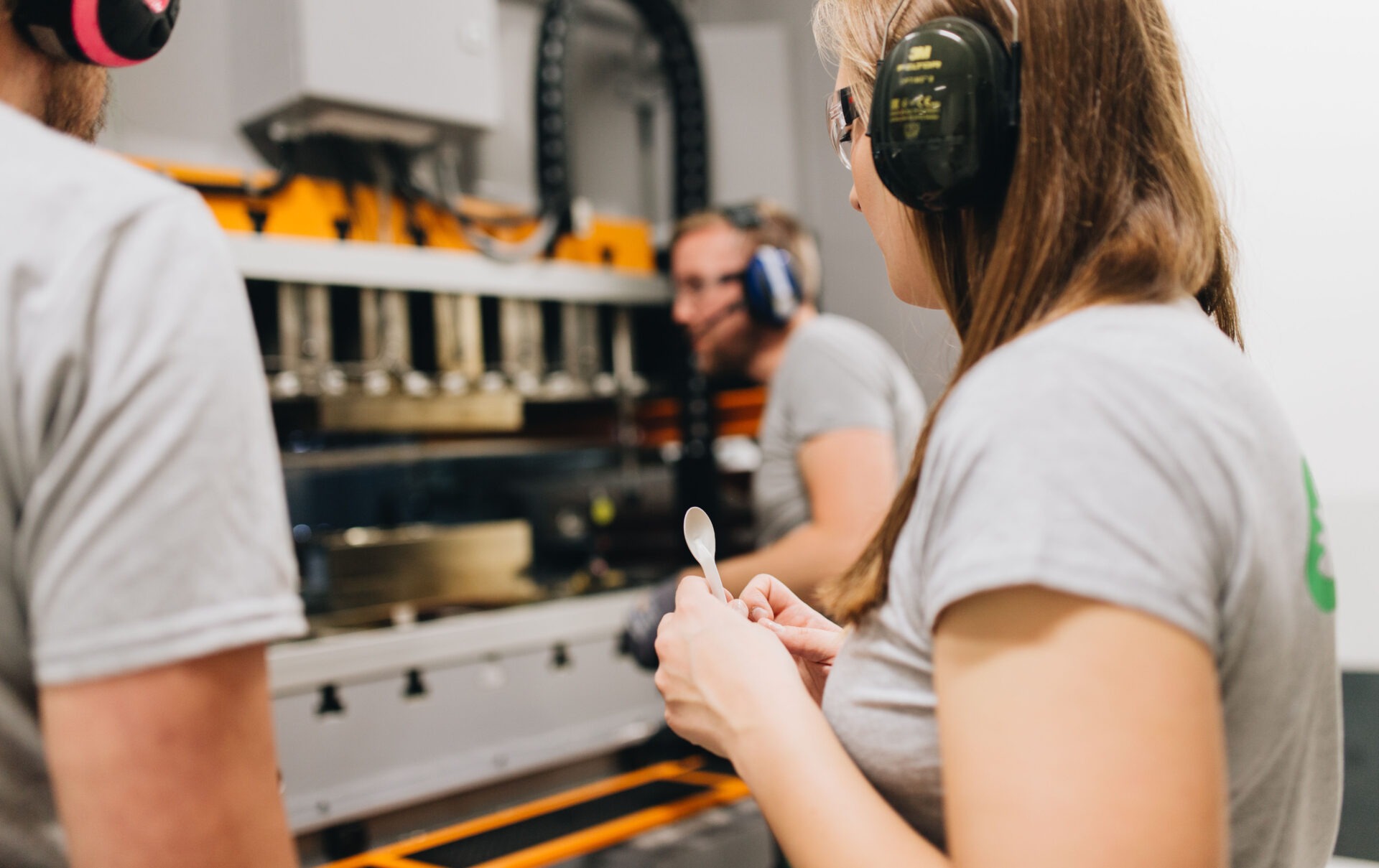
PulPac expands its sustainability-driven mission with local US operations
The US expansion is a strategic move that aims to bring PulPac’s sustainable solutions closer to the market, supporting the company’s vision of creating a more sustainable future.
PulPac expands its sustainability-driven mission with local US operations, application development, and a demonstration production site in partnership with Curt G Joa.
Swedish innovative packaging company, PulPac, announces an expansion of its mission-driven operations today. Following the partnership with Curt G Joa (JOA) to set up a more significant demonstration site for Dry Molded Fiber, PulPac wants to establish its own US operations in the Upper Mid-West region. The expansion includes a dedicated application development team and a state-of-the-art sampling facility to accelerate both product innovation and customization.
The US expansion is a strategic move that aims to bring PulPac’s sustainable solutions closer to the market, supporting the company’s vision of creating a more sustainable future. The collaboration with JOA, a leading machinery manufacturer for the hygiene and disposable products industry, and PulPac’s ongoing partnership with Seismic Solution , is a significant step toward scaling up the manufacturing process and offering customers a complete solution for sustainable packaging.
“We are thrilled to expand our mission and offer our sustainable packaging solutions to the US market”
— Linus Larsson Green, CEO of PulPac
PulPac’s patented Dry Molded Fiber technology is a groundbreaking manufacturing process for turning renewable pulp into high-performance packaging materials that are fully biodegradable, recyclable, and compostable. The Dry Molded Fiber manufacturing process has a lower climate impact than wet-molding and plastic processing. And it provides the packaging industry with a solution for a swift transition toward circularity to tackle the sustainability challenge the industry is facing.
“We are thrilled to expand our mission and offer our sustainable packaging solutions to the US market,” says Linus Larsson Green, CEO of PulPac. “Our local operations and partnership with JOA enables us to accelerate our innovation efforts and bring our sustainable products closer to our customers. We are committed to creating a circular economy and providing sustainable solutions that benefit the planet and people,”
The expansion is a testament to PulPac’s commitment to innovation and sustainability. With dedicated local US operations, an applications development team, and a demonstration site with JOA, PulPac is on the verge of revolutionizing the US packaging industry with a brilliantly simple technology that meets both customer needs and environmental challenges, as well as the industry’s need for scalable and economically sustainable solutions.
Media Contacts
Sanna Fager, Chief Commercial Officer PulPac, sanna.fager@pulpac.com
Ann Dynehäll, Chief Communications Officer PulPac, ann.dynehall@pulpac.com
About PulPac
PulPac provides the packaging industry with groundbreaking manufacturing technology for making economical, high-performance fiber-based packaging and single-use products. By pioneering the technology of cellulose molding, PulPac enables its customers to replace single-use plastics with sustainable and cost-competitive natural fiber alternatives globally. For additional information about PulPac, please visit www.pulpac.com or follow us on social media.
Dry Molded Fiber
The Dry Molded Fiber process, invented and internationally patented by PulPac, is a manufacturing technology designed for the emerging circular economy. By leveraging globally available, affordable, and renewable commodity cellulose fiber, Dry Molded Fiber technology allows for producing high-performance fiber-based packaging with highly competitive unit economics. Dry Molded Fiber also saves significant amounts of valuable water resources and energy, resulting in up to 80% lower CO2 footprint than alternatives. Dry Molded Fiber processing is up to ten times as efficient as conventional fiber molding processing, first used over 100 years ago.