
Dry Molded Fiber
Driving packaging sustainability forward
With cost-effective, high-speed, and resource-efficient production that lowers carbon footprint, Dry Molded Fiber is the ideal solution for companies looking to replace single-use plastics or expand their portfolio of responsible packaging.
Fiber was always the best alternative – we just made it better
Like all great innovations, the Dry Molded Fiber technology was the next logical evolution. Instead of creating a fiber slurry, we form a dry web of fibers, minimizing water use in the molding process. This allows us to achieve cycle times as fast as 3.5 seconds, reducing both water and energy consumption while maximizing output and minimizing environmental impact.

aspects of
Dry Molded Fiber process
Main resource is generic and available worldwide
Start with pulp
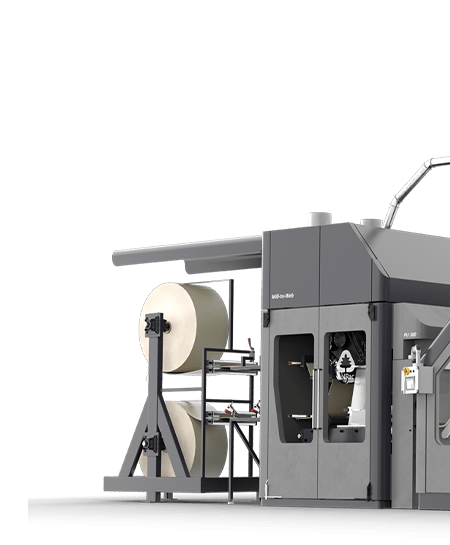
The pulp is milled and fibers are air-laid into a dry web
Mill-to-web
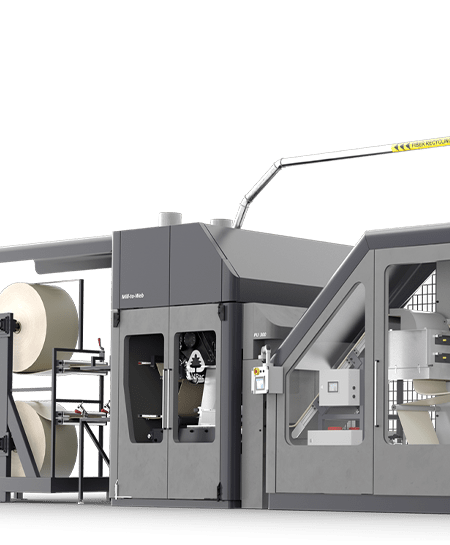
Barriers are applied to meet product requirements and intended use
Apply barrier
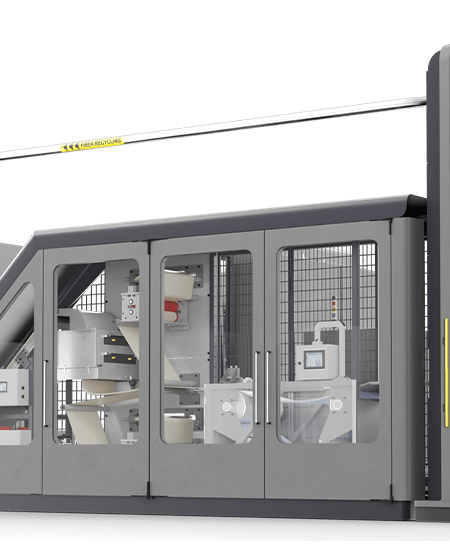
Products are formed using heat and pressure in standard plate press with uniquely designed tools
Mold into product
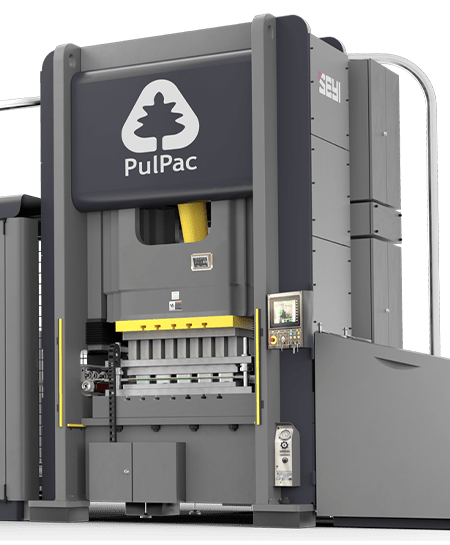
All excess material is fed back into the process
Recycle waste
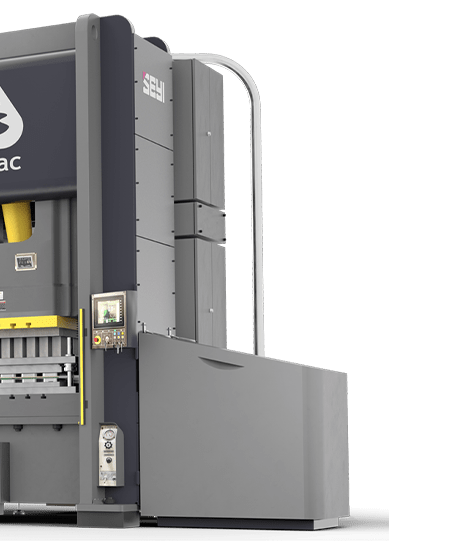
Explore Dry Molded Fiber
Complement your existing packaging production
Whether you’re in plastic conversion or traditional fiber forming, Dry Molded Fiber offers benefits and allows you to expand your portfolio with renewable, recyclable, compostable, and biodegradable packaging—helping you meet sustainability goals without compromising on performance.
This technology enables high-speed production in a streamlined process, converting raw material to finished products in a single machine. It offers a unique combination of benefits—whether for large-scale production, custom orders, specific design needs, or optimizing factory footprint.
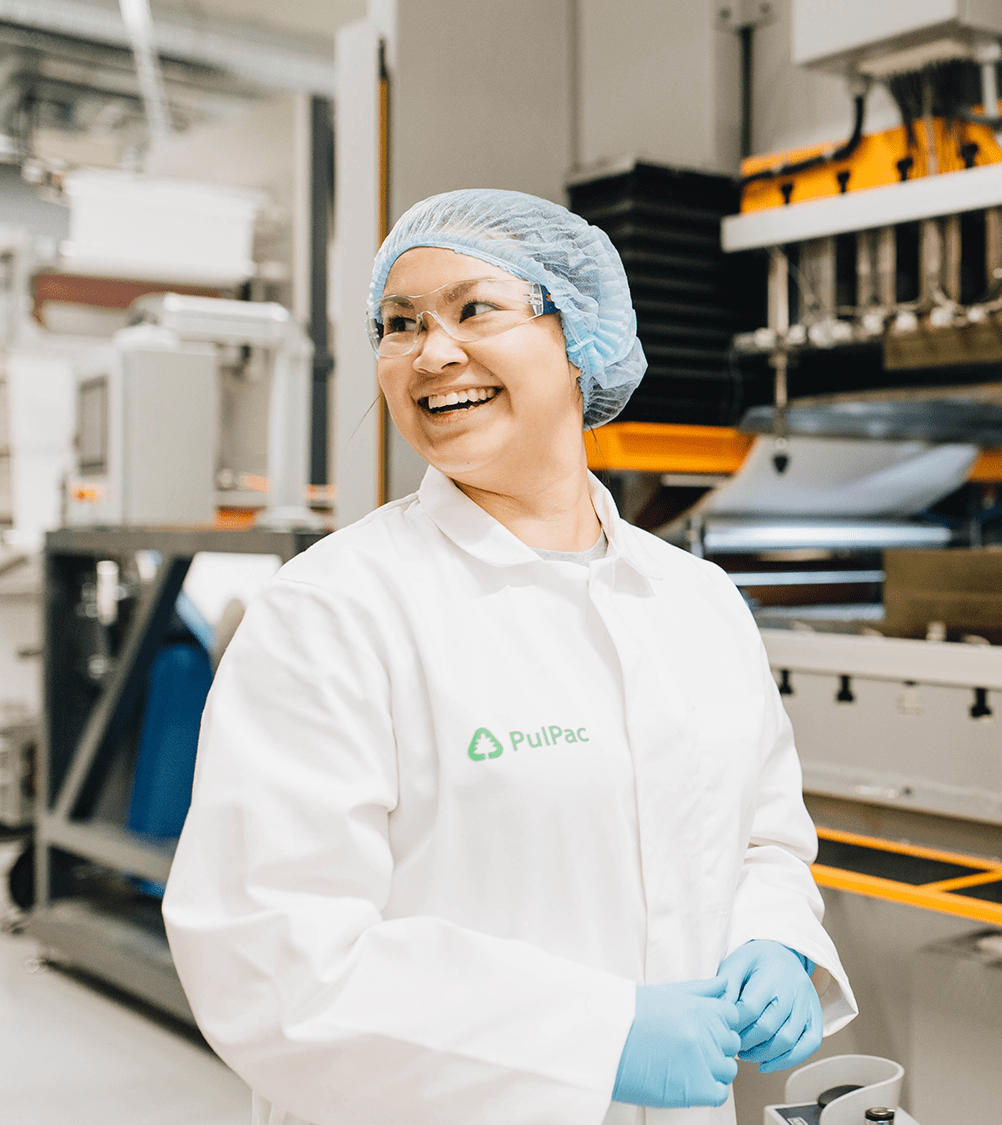
TECHNOLOGY LICENSING
Implement Dry Molded Fiber in your operations
Our inclusive, future-proof licensing model empowers businesses to adopt Dry Molded Fiber and drive positive change across the packaging industry – with world-leading expertise and support from us and our network of partners included
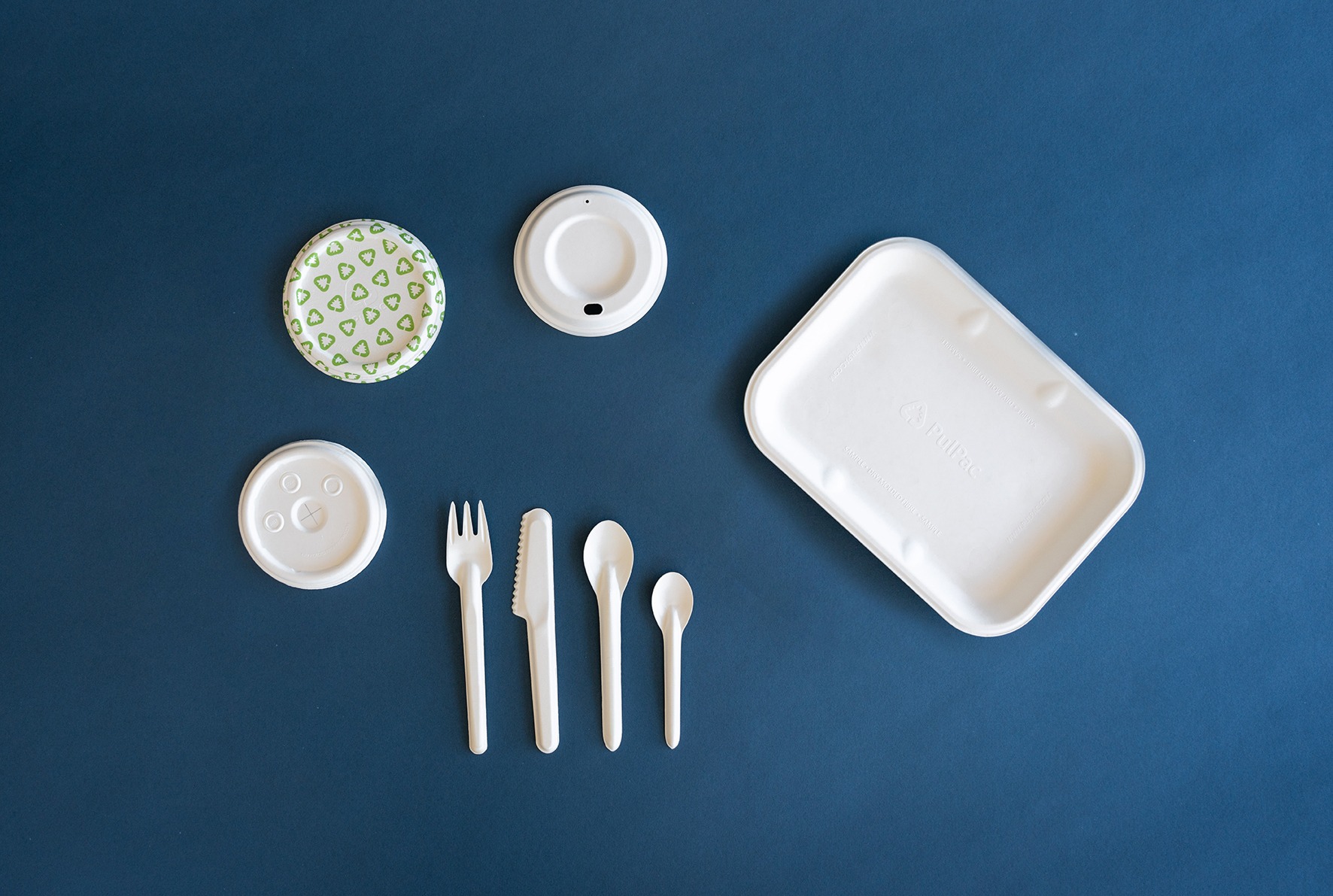
STANDARDIZED OR CUSTOMIZED
We help you develop your Dry Molded FIber product
Adapt existing product lines or design unique products to provide responsible packaging that meets today’s demands for sustainability and convenience, while offering a scalable solution for tomorrow.
How
to get started with Dry Molded Fiber?
Start at your own pace: evaluate the technology, integrate it with existing production, or scale to full capacity.